Things you must know about injection molding
What is plastic injection molding ?
We live in a world surrounded by plastics. 60% of daily products are made in plastics.
And the most commonly way to manufacture the plastic products is ” Injection molding ”.
The injection molding process requires the use of an ”injection molding machine”, ”raw plastic material”, and a ”mold”. The plastic is melted in the injection molding machine and then injected into the mold, where it cools and solidifies into the final part. The steps in this process are described in greater detail in the next section.

Plastic material
Semi-crystalline 結晶性材料塑膠: PP,PE,PA
Amorphous 非結晶性材料塑膠:PS,ABS,PC,PVC
(Learn more about plastic material Different types of plastic materials)
Plastic injection Mold
Hot runner mold
Cold runner mold (two plate or three plate)
( Learn more about hot runner vs. cold runner Cold runner vs Hot runner )
Plastic Injection molding machine:hydraulic, electric, and hybrid.
Structure of injection molding machine
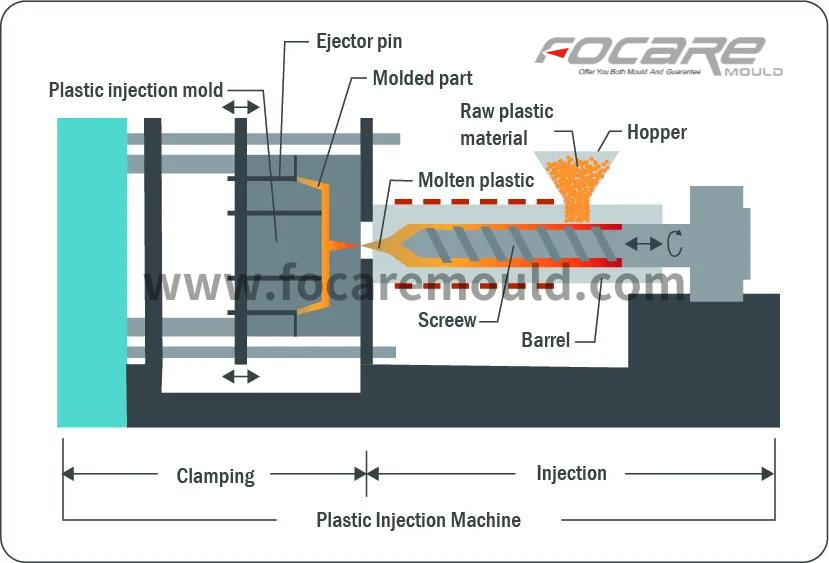
Hopper : Where the plastic material is poured into the machine before the injection molding process can begin.
Barrel : The barrel of the injection molding machine supports the reciprocating plasticizing screw. It is heated by the electric heater bands.
Screw : Reciprocating screw. The reciprocating screw is used to compress, melt, and convey the material.
Mold : Injecting plastic materials molten by heat into a mold, and then cooling and solidifying them.
Ejector pin (part of mold not machine) : Ejector pins help safely remove parts from molds after they have been made.
The process of making plastic products by injection molding
STEP 1: THE MOLD CLOSES
The Injection Molding cycle timer begins when the mold closes.
STEP 2: INJECTION
The heated plastic is injected into the mold. As the melt enters the mold, the displaced air escapes through vents in the injection pins and along the parting line. Runner, gate and vent design are important to insure the mold is properly filled.
STEP 3: COOLING
Once the mold is filled the part is allowed to cool for the exact amount of time needed to harden the material. Cooling time is dependent on the type of resin used and the thickness of the part. Each mold is designed with internal cooling or heating lines where water is cycled through the mold to maintain a constant temperature.
STEP 4: PLASTICIZING THE RESIN
While the part cools, the barrel screw retracts and draws new plastic resin into the barrel from the material hopper. The heater bands maintain the needed barrel temperature for the type of resin being used.
STEP 5: EJECTION
The mold opens and the ejector rod moves the ejector pins forward to push the final product out.