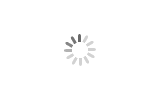
Oil Bottle Plastic Cap Plastic Injection Mould
Brand :Focare
Product origin :China
Delivery time :60 days
Supply capacity :500 molds per year
The unscrewing device of this cap mold is hydraulic motor. The ejecting sequence of this cap mold is to let the upper press plate open the mold first, and rely on the I-shaped block to drive the cavity slider to slide away. The mold is opened to a certain stroke, and the caps will be unscrewed by hydraulic unscrewing motor. The left and right thimble plates are performed simultaneously. The spring is pushed out of the barrel by the force of the spring, so that the product is firmly in the core part. After opening the mold, the oil cylinder pushes the rack, drives the central drive shaft, drives 4 product threaded shafts backward to disengage the product, and then relies on the 2 ejector rods on the outside of the machine, and the ejection plate pushes caps off from mold.
When internal or external threads are required on a plastic cap, unscrewing or rotating core molds are utilized. In order to actuate the rotating cores, different drive systems can be incorporated in the mould design. The action is coordinated with the moulding machine cycle so that extraction occurs when the mold is opened.
The mold of this oil bottle cap is designed with unscrewing device. For unscrewing device, it could be driven by electric motor or hydraulic motor.
1. Electric Motors / Gear Motors
The main properties of an electric system are well known. Typically, an electric motor is rather fast but its torque is not on the highest side. New servo-motors partly overcome the lack of torque.
The simple control of an electric motor is easy and cheap, while a sophisticated drive can be costly. It has the advantage of precisely controlling position, speed and acceleration, being good for fast cycles where the required torque is not too high. Of course, a very precise position for the end-of-stroke implies a very precise control, which may increase the cost. An alternative is the use of mechanical (and adjustable) stops for the end-of-stroke. With a drive, the end-of-stroke speed will be low and the parts will not hit each other hard.
For multiple cores, a train of gears is required, or a pulley/belt system as in the last picture. Normally this does not allow for very high torques. This system is fairly compact and can fit in tight spaces, but the electric motor must be kept away from areas having a very high temperature. This is especially true when belts are used. The electrical connections are often on the side, and this may be inconvenient in some type of molds. This is clearly the most natural solution in electric presses.
2. Hydraulic Motors
In many ways, these devices are similar to electric motors, with the exception that the driving ‘agent’ is a fluid and not electricity, so their use on hydraulic presses comes natural.
Basically, they have the same pros and cons of electric motors. They are usually rather fast, and torque is generally higher than electric motors. They are normally slower than electric motors, and they often don’t require a gear reducer. If a precise end-of- stroke position is required, a proportional valve has to be used, together with some detection system. All that adds to the cost, especially if we include mechanical stops.
As for electric motors, a train of gears is required in the case of multiple cores; the system is rather compact but oil connections are often on the side, therefore increasing overall dimensions. Operative temperatures are the same as those of normal hydraulic cylinders. Some manufacturers sell ready-to-use units
The unscrewing device of this cap mold is hydraulic motor. The ejecting sequence of this cap mold is to let the upper press plate open the mold first, and rely on the I-shaped block to drive the cavity slider to slide away. The mold is opened to a certain stroke, and the caps will be unscrewed by hydraulic unscrewing motor. The left and right thimble plates are performed simultaneously. The spring is pushed out of the barrel by the force of the spring, so that the product is firmly in the core part. After opening the mold, the oil cylinder pushes the rack, drives the central drive shaft, drives 4 product threaded shafts backward to disengage the product, and then relies on the 2 ejector rods on the outside of the machine, and the ejection plate pushes caps off from mold.